ISO9001认证质量管理体系认证
ISO9000认证申请质量管理体系认证申请
ISO9001认证顾问质量管理体系认证顾问
ISO9001认证培训质量管理体系内审员培训
ISO9001认证咨询质量管理体系建立指导
ISO9001认证辅导质量管理体系认证申请
材料顾问协助整理
资料咨询依据标准整理
条件依据标准核定
前提辅导前判断
1 文件化信息控制程序
2 公司环境分析程序
3 信息沟通控制程序
4 风险与机遇管理程序
5 管理评审程序
6 不良质量成本控制程序
7 经营计划控制程序
8 人力资源管理程序
9 公司知识管理程序
10 设备管理程序
11 顾客要求控制程序
12 APQP控制程序
13 FMEA控制程序
14 MSA控制程序
15 SPC控制程序
16 P**控制程序
17 工程变更控制程序
18 外部供方管理程序
19 标识和可追溯性控制程序
20 生产过程控制程序
21 仓储管理程序
22 顾客及外部供方财产控制程序
23 监视与测量设备控制程序
24 顾客满意度调查控制程序
25 顾客服务控制程序
26 产品的监视和测量控制程序
27 内部审核控制程序
28 不合格品控制程序
29 绩效评价管理程序
30 纠正与预防措施控制程序
31 产品安全控制程序
32 应急计划管理程序
33 法律法规管理程序
呆滞料处理
除特定物料外,一般物料、成品若发生以下任何一项均视为呆滞料:
保存三个月;
订单取消或判定无法使用;
因物料变更,BOM修改后无法利用;
制造过程产生边角料。
由信息课稽核员每月15号应导出**过90天未动的物料清单,经PMC物控确认,认为短期内无法再利用的,后,以邮件通知资材及信息课.
由资材课先做实物的库区调整,调整完成后通知信息课做K3帐务的调整.
呆滞料处理由资材单位整理,会同物控、品管、技术、采购等单位进行评估后进行处理,处理方式主要有:
(1)代用或加工后代用(2)拆退回收(3)报废等
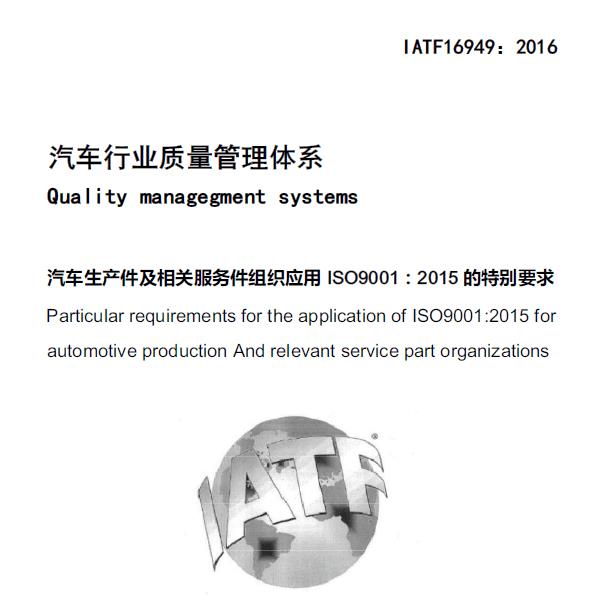
其它部门零星领料
由需求部分填写《内部联络单》,经部门主管批准后发至PMC,由相关物控确认后,再由PMC计划员发至各录入员打单.
《其它出库单》打好后,由领料单位至物控确认后实施领料.
《内部联络单》或相关依据性的文件需料号,数量此信息在物控确认后不可随意更改.
如属其它事业部调拨物料,则应事先发书面通知PMC,由物控组织好材料后,PMC下销售订单,由资材打《销售出库单》办理领料手续.
在K3中零星物料有“以旧换新”的要求物料在领用时,用旧的工具、物料来更换,更换后的工具、物料由资材保存,待月底时统一交行政进行处理
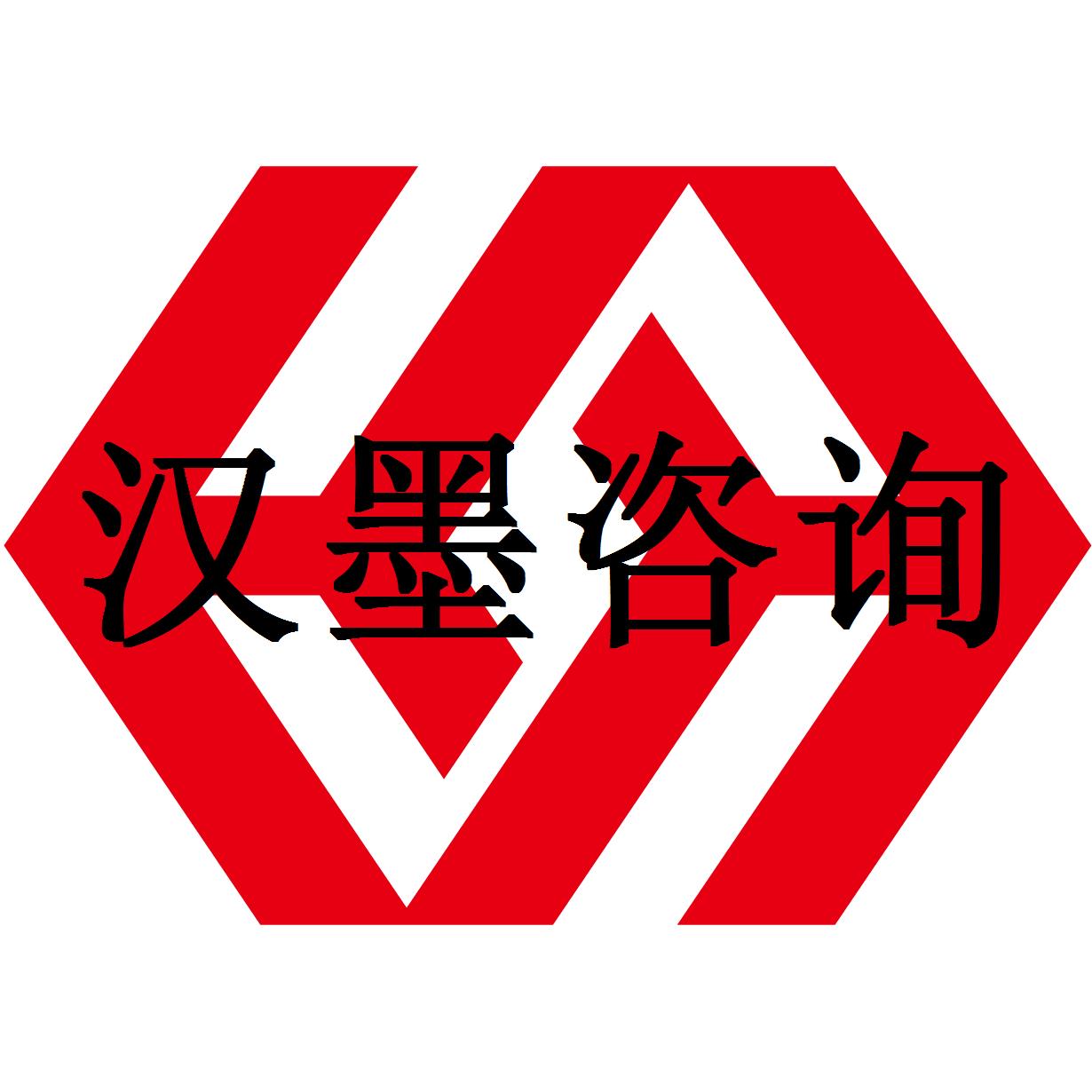
合同/订单的签订和执行
与顾客签订的合同,由业务部确认能够满足顾客的合理要求时,由业务部代表公司在客户原订单上签字盖章回传作为评审的记录。
业务内勤将评审接受的订单转给仓库进行库存品的盘查,要求仓管员在客户原订单后上后再返回业务内勤,或通过电子表话方式进行确认库存品数量。业务内勤根据公司规定的产品多投量、订单要求量、库存品数量核算本单产品的生产投产量,编写“生产制造令”呈副总经理或其授权人(厂长)签核后下发生产部、采购、品管。
如果接到是客户的“排程表或周计划”下单时,业务可以考虑不需转化成公司“生产制造令”时,可将客户的“排程表或周计划”复制转发生产、品管、资材相关部门执行。
各部门依据生产任务单要求进行生产计划安排和跟踪、采购计划安排、产品实现过程的控制。
生管或内勤业务跟踪生产部各工序的进度,保证生产计划与出货计划顺畅进行。
生管或内勤业务根据订单完工情况、客户交货要求、运输途径等编写“出货预排表”安排产品出货。
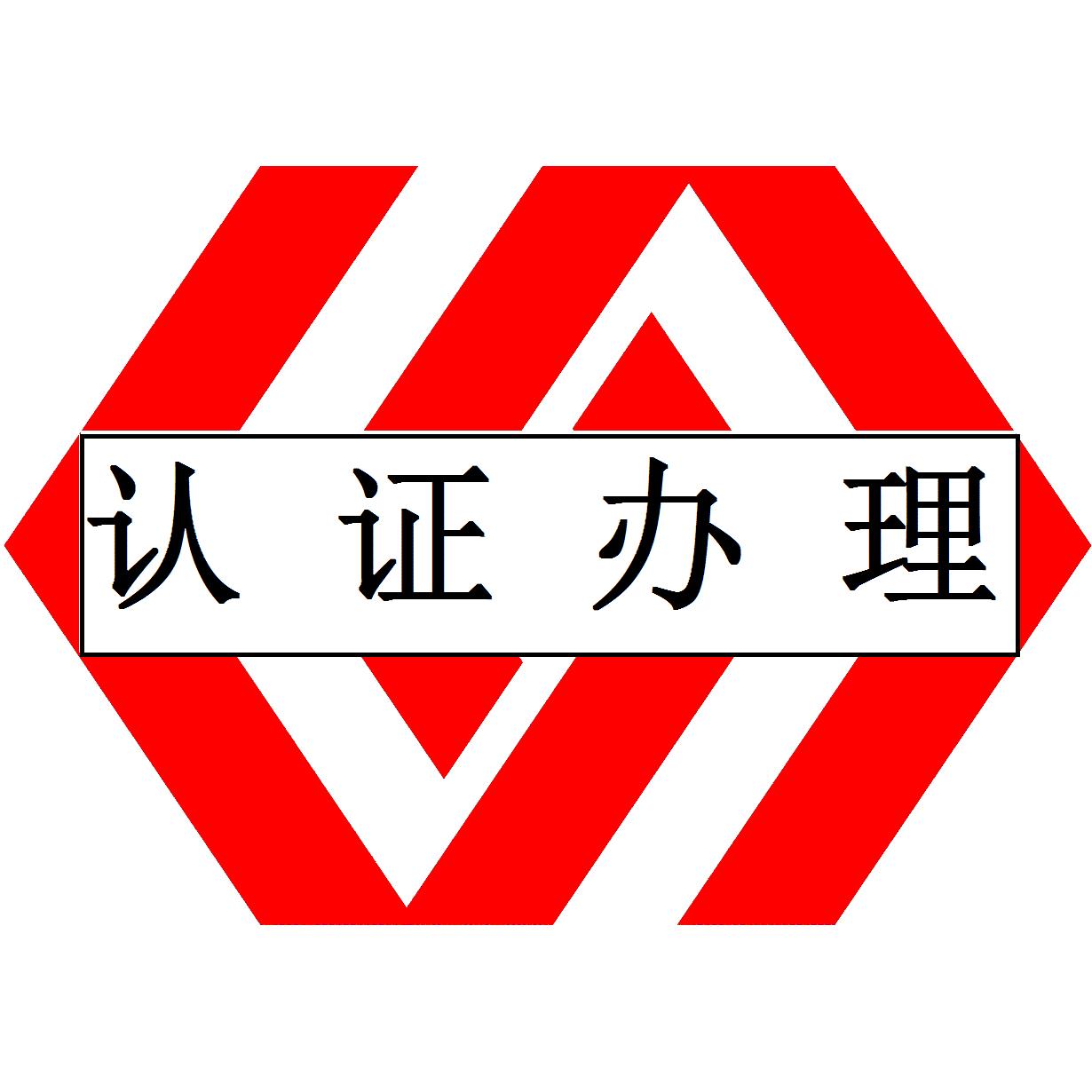
仓储管理
物料未经品管检验或判定合格不得办理入库手续,应暂存于待检区域。对于让步品要明确标识,要与合格品区分存放。当品管检验结果为“不合格”时要立即通知资材对该批物料进行隔离,张贴“不合格”标签,未经允许不可随意处置。资材应尽快办理退货手续。ROHS标准的物料要做好区分与标识,不得与其它物料混放。
所有物料存放区域均有“物料卡”且需放置于显著位置。牌上所写的“存放位置”一栏应与K3系统上的“缺省仓库”一致,不得随意更改。若遇资材区域调整,应该立即以书面形式通知信息课对系统做调整。
同类物料或同一批物料应以集中存放为原则,如因场所限制不能达到上述要求,应在“物料卡”上其它存放区域的代号,以便查找。
物料从地面叠放高度不得**2.5M,货架上叠放高度不得**过2M,以不损坏物料品质为原则。
物料以先出为管理原则,先入库者**发放。**过保质期或在仓库存储时间**过6个月的物料要用于生产时,由资材课办理重新送检工作,经品管确认可用后方可发放.
物料进出严格依凭证作业,如单据上有错误,应立即反馈组长调查处理,物料入库应严格依采购订单控制到货数量,对于**交的要责令供应商取回或交由采购协调解决。
只要物料异动发生,即登录物料卡、K3帐须于当日登记完成,以确保帐、物、卡一致。
对于常用物料必须由物控、采购等单位协商拟定低及高库存量标准,呈请事业部总经理核准实施,以保证安全库存量,后续应每半年重新核定一次,酌情调整。
使用多方论证方法的方面包括:
a.项目管理(例如:APQP)。
b.产品和制造过程设计活动(如:DFM和DFA)。
c.产品设计风险分析(FMEA)的开发和评审,包括降低潜在风险的措施。
d.制造过程风险分析(如:FMEA、过程流程、控制计划和标准的工作书)的开发和评审。
http://linfujia.cn.b2b168.com