资料顾问整理
材料辅导协助
周期120天左右
IATF16949认证顾问汽车质量管理体系认证辅导
IATF16949认证申请质量管理体系内审员指导
IATF16949认证咨询汽车质量管理体系认证申请
IATF16949认证辅导IATF16949认证内审员培训
阶段
基础调研与体系诊断
1.公司营运现场调研,确定质量管理状况,与管理人员沟通了解企业运作
2.体系诊断,与管理人员确认体系运行状态与期望
3.成立体系推进会
4.体系范围确认 无
问题点 企业质量管理基础比较薄弱
老师交办事项 下次工作内容
体系推进会的人员必须确认,并且相关人员要比较稳定;
体系推进会必须先把标准看一遍 讲解IATF16949标准
风险顺序数(RPN):风险顺序数是严重度(S)、频度(O)和探测度(D)的乘积。即: RPN=S×O×D。RPN取值在“1”到“1000”之间。
对设计中所有担心的事项可以用RPN值来排序。设计负责计算风险顺序数RPN,输出《产品设计/过程设计风险评估表》。
① 当RPN>50(或依顾客要求)时,应采取改进措施。
② 不管风险顺序数是多少,当S≥8时,都要采取改进措施。
建议的措施:
当失效模式按RPN值排出先后次序后,应先对排在前面的问题和关键的项目采取纠正措施。任何建议措施的目的都是为了减少严重度、频度和探测度的数值。如果对某一特定原因无建议措施,那么就在该栏中填写“无”,予以明确。应考虑以下措施。
① 为了减小失效发生的可能性,需要修改设计。
② 只有修改设计,才能减小严重度数。
③ 为了增加探测的可能性,需要修改设计。
④ 积的纠正措施是制订性的改进措施,以及采用统计过程控制(SPC)方法制订预防缺陷发生的措施。
责任及目标完成日期:填入建议措施的部门和个人,已及预定完成的日期。
采取的措施:当实施一项措施后,简要记录具体的措施和生效日期。
措施结果:当明确了纠正措施后,估算并记录措施后的严重度、频度和探测度, 计算并记录纠正后的RPN值。如未采取什么纠正措施,将措施后的RPN栏和对应的取值栏目空白即可。
所有纠正后的RPN值都应评审,而且如果有必要考虑进一步的措施,还应重复6.3.19到6.3.21的步骤。
跟踪:
品管应负责保证所有的建议措施已被实施或已妥善地落实。
FMEA是一个动态文件,它不仅应体现新的设计水平,还应体现新的有关纠正措施,包括产品正式投产后发生的设计更改和措施。
PFMEA的管理:完成的PFMEA有管理部负责归档保管,如须分发、更改和回收按《文件控制程序》规定执行。
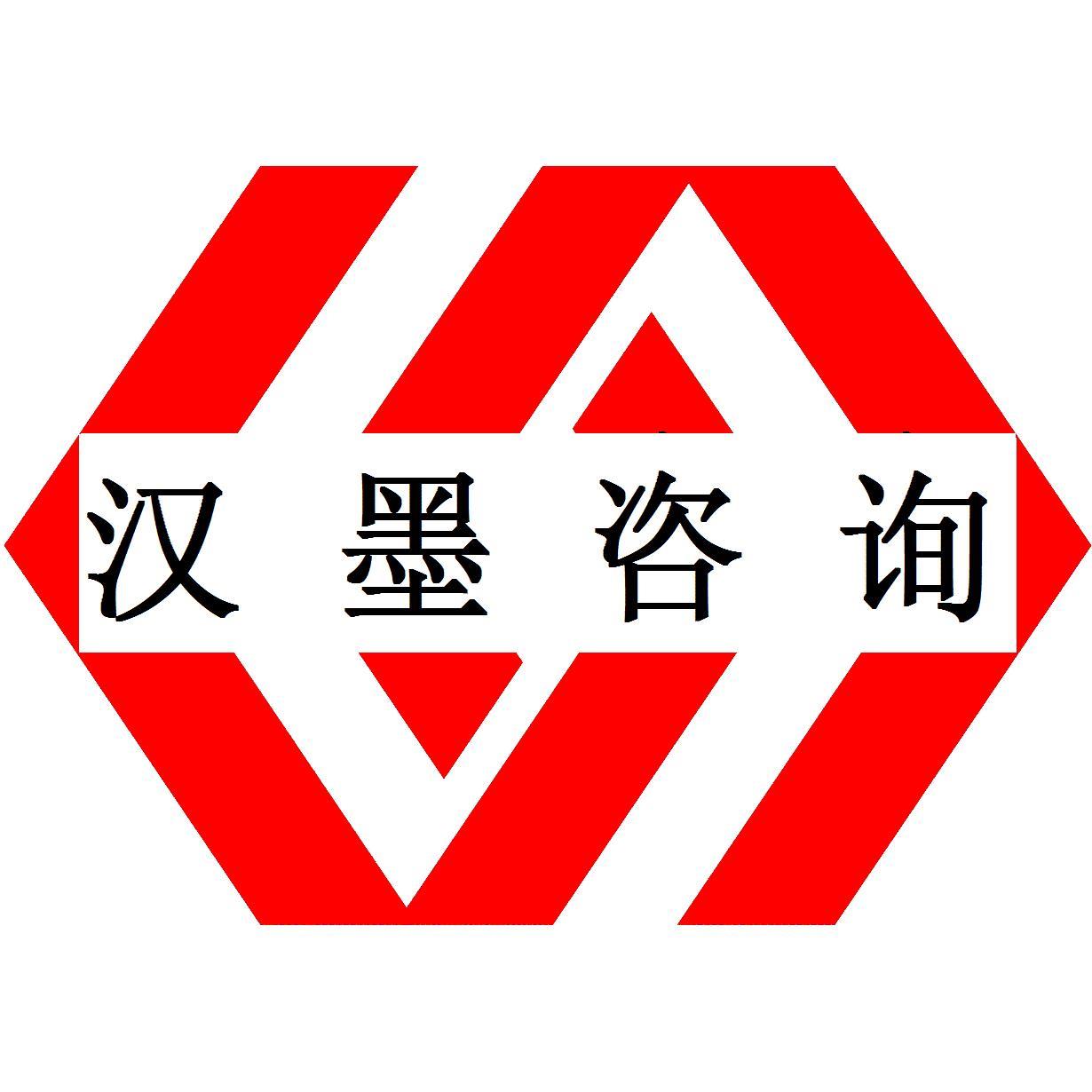
企业应定期开展生产一致性评审活动。
当生产一致性保证能力(包括人员能力、生产/检验设备、原材料和零部件总成、供应商、生产工艺、作业环境、管理体系等)发生重大变化时,企业应按照技术状态管理办法,对产品生产一致性实施控制,应有充分证据表明产品仍能满足批量生产一致性的控制要求。
当产品技术状态发生变更后,企业应按照有关程序文件对产品技术文件进行审核、批准,同时应按照《公告》管理规定办理产品变更或扩展手续,以确保批量产品的生产一致性。" "1、企业应按照技术状态管理办法,编制生产条件变更管理程序或流程,对批量产品的生产一致性实施有目的、有计划、有步骤的管理。管理内容包括生产条件的技术状态识别(标识)、控制、纪实和审核。其中,技术状态识别(标识),主要指产品结构和技术状态项目的选择确定、项目文件、编码、技术状态基线(技术状态时间点)建立等四方面内容。技术状态基线与对其批准的更改,共同组成批量产品现行批准的技术状态。
2、此外,应按照《公告》管理规定办理产品变更或扩展手续,以确保批量产品的生产一致性。
3、按照文件规定,由定期从质量、成本、生产能力、技术条件等多方面,评估企业生产一致性。
4、对于企业生产条件变更建议可行时,应组织试生产活动,通过样车符合性对变更条件后的生产一致性予以验证。" "1、查阅公司相关生产条件变更管理程序或流程文件;
2、查询近期公司人、机、料、法、环等方面主要因素的变化情况,查阅有关的评审记录及结果。
3、调阅产品《公告》参数,对照在产车辆变更后是否及时办理申请产品变更、扩展手续。" 生产一致性评审会议记录:高层、生产/检验设备、原材料和零部件总成、关键供应商、生产工艺、作业环境、管理体系发生重大变化时召开 5.6管理评审
《过程变更控制程序》、过程变更执行记录 7.2.2与产品有关要求的评审7.3.7设计和开发更改的控制
《产品变更控制程序》、产品变更执行记录,公告变更和管理 7.3.7设计和开发更改的控制
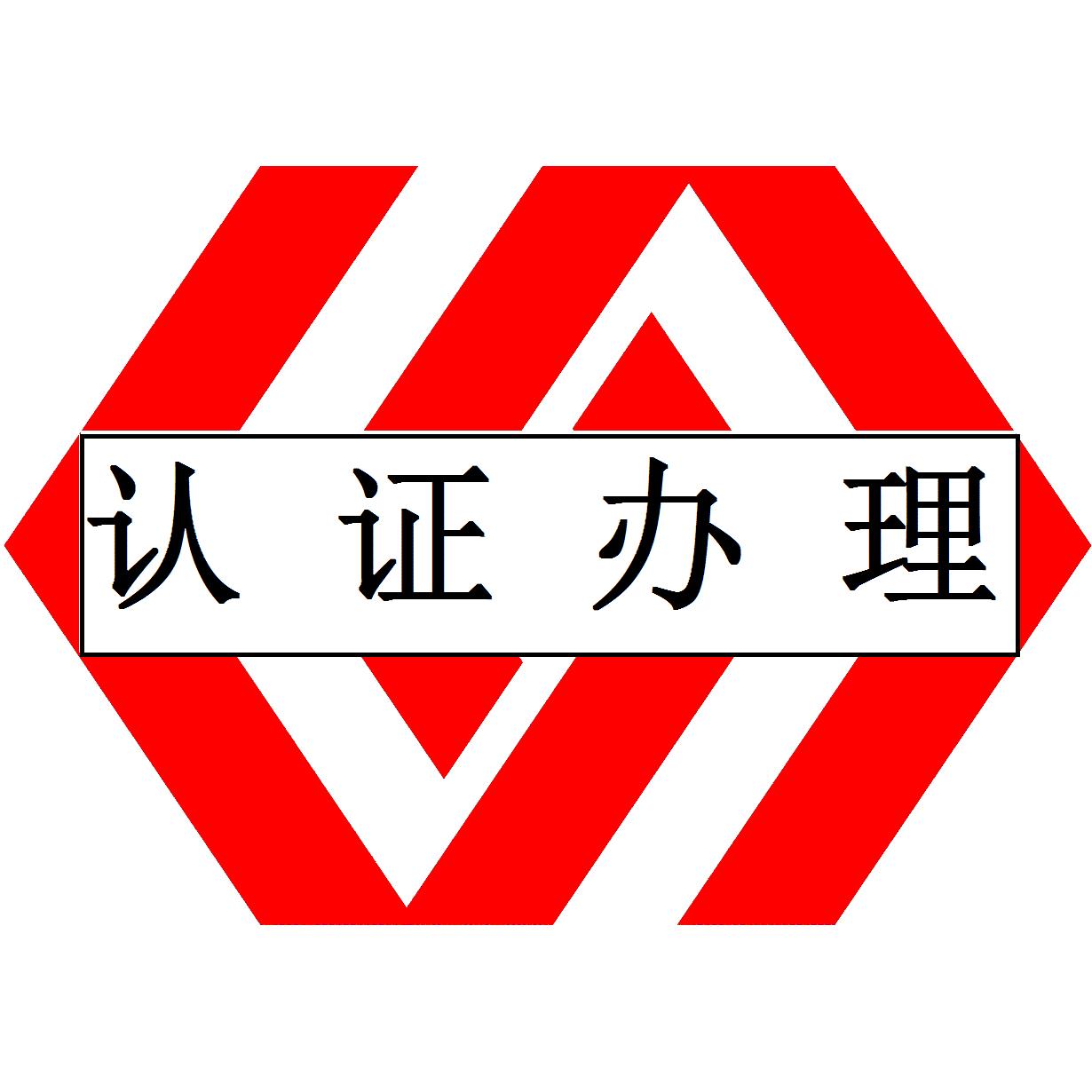
现行设计控制:列出预防措施、设计确认/验证或其他活动,这些活动的完成或承诺将确保该设计对于所考虑的失效模式和/或机理来说是充分的。现行的控制
方法是指已经用于或正用于相同或相似设计中的方法。应尽可能的把重点放在设计控制的改进上,如在实验室进行新系统试验、或创建新的系统模型化运算法等。
有两种类型的设计控制特性可以考虑:
A、预防:预防起因/机理或失效模式的发生,或减少它们的频度;
B、探测:在该项目投产前,以任何解析的或物理的方式,查出失效或失效模式的或起因/机理。
如有可能,**选用种的预防控制方法,让预防控制方法作为设计意图的一部分,因为其将影响到初的频度;初的探测度将基于失效起因/机理探测或对失效模式探测的设计控制。
探测度(D):是指零部件、半成品、成品、在安装使用前,利用现行设计的控制方法找出失效起因/机理过程缺陷的可能性的评价指标;或利用控制方法找出后续发生的实效模式的可能性的评价指标。评价等级分为“1”到“10”级,按严重程度递增。评价准则见表“3”。
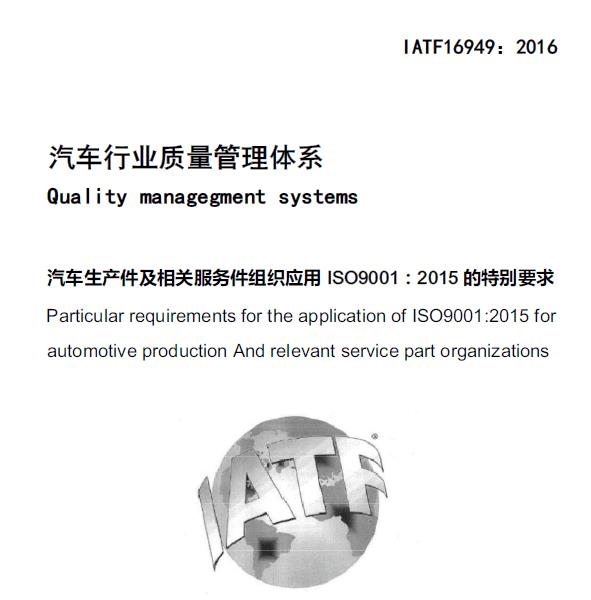
失效(Failure):指在生产过程中因人、机、料、法、参数异常及环境变化,..等造成产品的功能失效或外观不符合品保规范要求的现象。
失效问题分析:分析列出产品明确及潜在的问题。
制程失效模式与效应分析PFMEA:事**出制程中可能发生的错误与不良模式或变异,评估其影响与发生机率并且提出防止措失将对策标准化以降低生产品质风险的系统。
制程功能或需求:制程加工之目的。
失效模式:是指某一特定工序上出现过程失误时,如果没有被及时发现并纠正或清除,将出现失效后果的一种情形。
失效后果:潜在失效模式对产品可能造成的影响,含对当前工序的产品,对下一工序的产品和对客户会造成会有什么样的影响。
严重度S(Severity):评估失效模式所导致失效后果的严重程度。
失效原因:指失效模式是怎样发生的,并应依据可以纠正或可以控制的原则予以描述。
发生度O(Occurrence):问题发生频率的评价指针。
现行管制:目前已使用中的防止异常产生的生产对策措施或防止不良品流出的品质管理措施,区分为预防及侦测二种管制方式。
侦测度D(Detection):能够检出不良品防止流到下制程的能力评价指标。
1、各部门年度培训需求;
2、新员工入职、新员工上岗、在职员工技能提升、工种上岗前、调岗与转岗人员上岗前;
3、外训申请、培训申请表;
4、考评发现员工质量意识不足;
5、法律法规要求;
6、岗位知识要求;
7、顾客要求;
8、顾客沟通的能力要求;
9、员工行为准则;
10、社会责任;