ISO9000认证质量管理体系认证
ISO9000认证申请质量管理体系认证申请
ISO认证辅导ISO9000认证办理
ISO9001认证辅导质量管理体系认证辅导
ISO认证咨询质量管理体系认证咨询
ISO9001认证顾问质量管理体系认证顾问
所需资料顾问依据标准整理
审核材料咨询协助整理
周期30天左右
条件咨询把关
ISO9001认证培训质量管理体系内审员培训
执行了件检验,这是防止批量性不合格发生的有效措施
生产过程中主要检查项目明确
过程检验有建立巡检相关规定并有效执行
有日检验报告
无
生产设备符合生产的需求,有维护/点检
有维护计划和记录
建立了工序作业书
各工序作业书执行
有5S检查记录
建立了不合格控制程序
采取了及时有效措施临时处置不合格品,进行了原因分析并针对此类问题形成性措施。
设置了不合格品区域并建立不合格品处置流程
按照各类物料的自然属性、固体、液体消防和保管保养要求,实行分库、分区、分类分批堆放。每批货物应有状态标志及货位卡。
堆放要求:牢固、整齐、无明显倾斜、物品不得倒置。在库区底层的原辅料以及易受潮的包装材料必须有垫物架。
物料堆放应保持一定的距离。货与货相距0.2米,货与墙、地相距0.1米以上、离**0.5米以上。
标签按标签管理制度执行。
库存物资应每日巡视养护,确保无潮解、无霉变、无虫蛀、无鼠咬、无污染、无渗漏、无锈蚀、无燃爆,质量保持良好。
库存物资应按复检制度定期复检。
掌握物资库存情况,提供紧缺积压物资信息,并及时向有关部门反映。
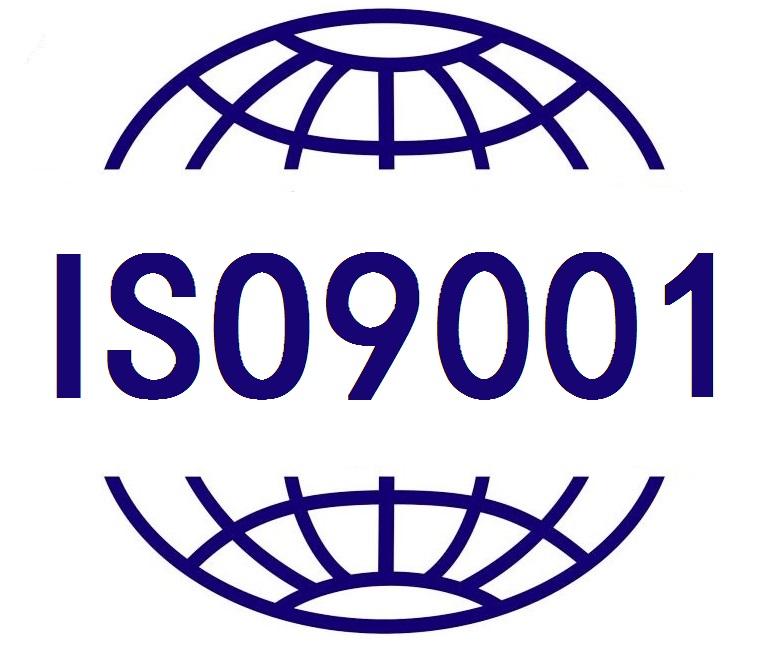
新供应商的选择
对于重要物资的供方或重要零部件的外协加工公司,由采购、生产部、品管部对其进行样品评鉴、小批试用,如果需要还可进行实地评鉴;
实地评鉴:对厂商之制造能力及品质管理能力进行实地了解评估,并于回公司后统计评估结果,填入“供方基本资料表”;评鉴为合格,由采购将评鉴结果呈副总经理核准。
样品评鉴:新供方根据公司提供的技术参数、要求提供样品,公司对样品进行验证,出具相应的“样品检验报告”或“样品试用报告”,经由品管主管审核后传回采购;由采购将样品检测的结果填入“供方基本资料表”;
样品经过检验合格后,如有必要采购部可要求供方进行小批量供货,小批量供货经品管检验合格后,生产部将小批量试用结果反馈采购部。供方评估资料完整,经副总经理批准可列入“合格供方名单”。
对于一般物资、物资的供方,本公司一般采用对其进行样品评鉴的方式,详情同5.2.2.1中的样品;
对于提供支持的供方一般只进行部分内容的调查或索取相关文件和资料的复印件即可;
对于提供设备备件、易损件、紧固件,生产办公用品及一次性业务往来的供方,由采购进行市场、商家比较即可采购供方无须列入“合格供方名单”;
供应商审核程序:
由采购负责收集新供应商资料:
A、收集资料方法可以是查询、问卷、实地到访、公司名册、商业登记、业绩报告或委托验
证等;
B、寻求供应商采购之前,提供“供应商基本资料表”作为采购的基本资料及质量体系保证依据。
各相关部门评审调查情况,由副总经理进行批准。
供应商终审核结果:
A、可成为公司的合格供应商;
B、备用供应商;
C、不合格供应商。
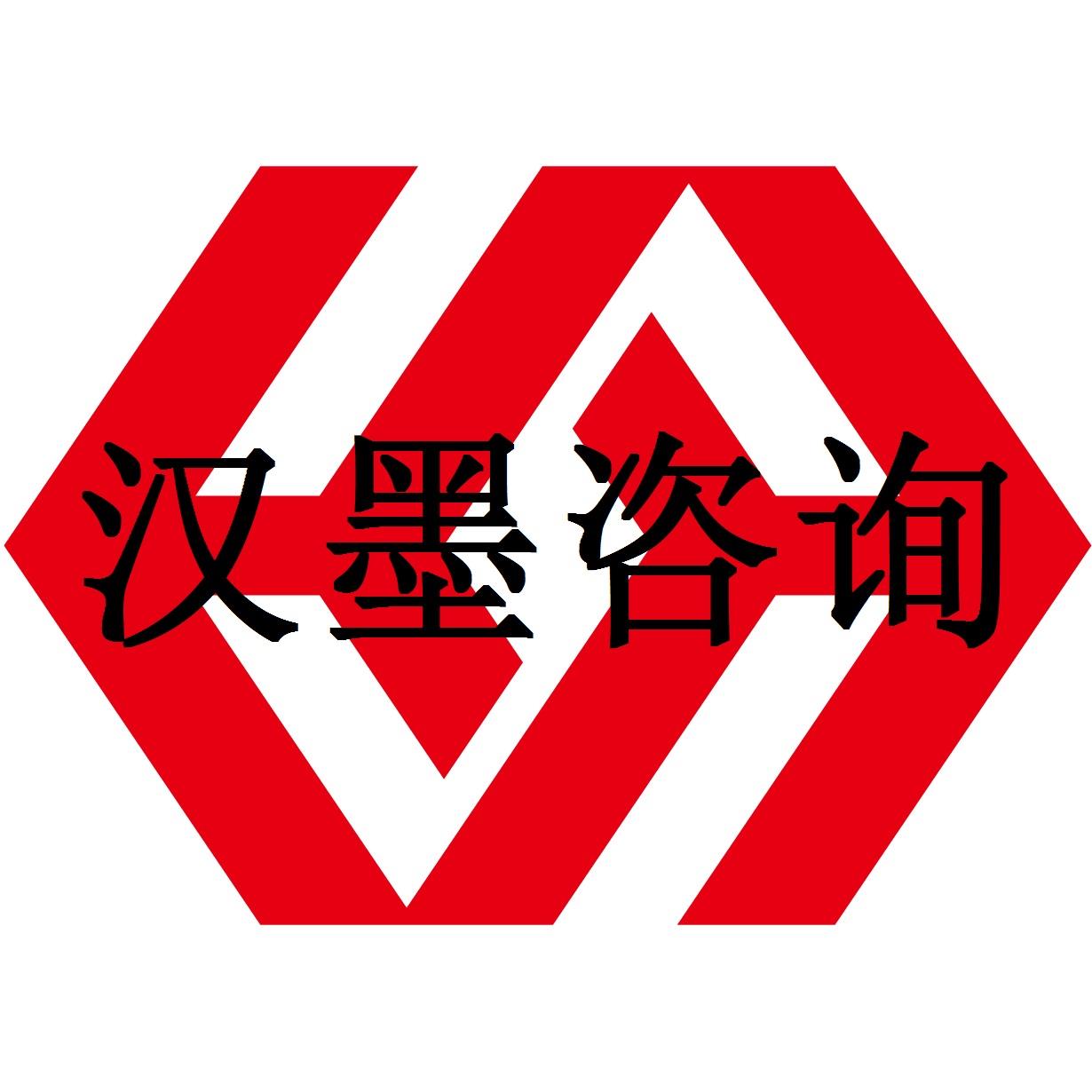
品管及生产车间按职责分工加强对生产过程的产品质量监督检验,严把每个过程的产品质量。做好:操作人员自检、品管员件检验、巡视检验及成品检验工作。并做好记录,做好检验状态的标识工作。具体《制程检验规范》操作
品管及生产车间在生产过程中发现不合格品要认真做好记录、标识、隔离,并及时处置。必要时责成责任部门或个人,分析产生原因,制订有效措施并实施,以防再度发生。具体按照[不合格品控制程序]规定执行。
工序完工产品应移入待检区,经过品管检验合格,加盖合格标识或品管员签认合格,产品方可放行下工序。
产品生产过程中做好产品的物料交接,上工序完成后应认真填写产品“产品交接单”并交品管确认签字,连同产品和交接单转交下一工序。接收工序应授权专人进行产品的验收,保证产品的质量符合要求和数量准确,并在产品交接单上签字确认。
生产计划监督
生产主管和业务内勤根据“生产制造令 ”、“生产日报表”核对计划的完成情况,编写“生产进度控制表”,并不定期进行现场检查,以掌握生产进度和现场状况;各车间根据生产任务单,认真组织生产,定期检查进度,发现问题及时协调解决,确保按质按量按时完成生产任务。
当生产进度延误时,生产部应立即进行分析、协调,必要时采取加班或向相关部门申请支援等措施加以弥补;
当生产进度延误,需报告业务内勤和业务部与顾客协调,必要时由业务部负责对事件评估及协商交货期事宜。
生产批完工总结
生产部整批产品完工后,应做产品完工总结,分析订单交期是否按时完成、生产过程产品质量状况、产品是否产生余量(数量多少)、生产过程是否有异常、班组生产效率评价等。
业务内勤统计每月订单生产部的内部生产计划达成率、每批产品物料利用率、多投率等生产控制指标达成情况。
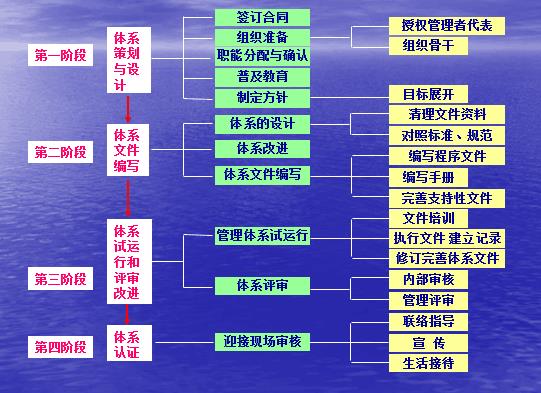
C1 市场需求的确定 S1 基础设施 M1 风险和机遇的应对措施
C2 产品和服务开发 S2 过程环境 M2 质量目标及其实施的策划
C3 产品生产和服务提供 S3 监视和测量设备 M3 顾客满意
C4 产品防护 S4 知识 M4 数据分析与评价
C5 交付后的活动 S5 能力 M5 内部审核
S6 意识 M6 管理评审
S7 沟通 M7 不符合和纠正措施
S8 形成文件的信息 M8 改进
S9 运行策划过程
S10 外部供应产品和服务的控制
S11 标识和可追溯性
S12 顾客或外部供方的财产
S13 产品和服务放行
S14 不合格产品和服务
在为产品和过程确定的要求的基础上,是否从总体上对可加工性开展了评价? 对于可加工性评价的步骤,必须加以规范。
必须对合同和询价文本的可行性开展检验。
必须有一道过程,通过它确定所有产品要求,包括那些客户没有明确说明的要求。
必须将经验(教训)以及针对未来的期望考虑在内。
在向客户报价前的审批过程必须加以规范。
所有相关负责/参与的部门必须确认客户要求的可行性(采购、研发、生产、质量、物流)
在报价阶段,就已经需要考虑到样件制造,原型件制造等需要的产能
- 产品/过程研发
- 客户要求、客户规范、产品责任要求
- 时间安排,时间框架
- 针对下级供应商权责关系的定义
- 规范,标准,法律,环保
- 产能、原材料到位情况
- 负责研发的有资质人员
- 生产加工可能,生产地点、建筑,空间
- 设备,模具,生产/检验工具,工具,实验室设备,运输工具,容器,仓库 QR8.3-05 NO. 202001 《小组可行性承诺报告》
QR8.3-04 NO. 202001 《项目可行性评审报告》
http://linfujia.cn.b2b168.com